The top 6 paradigms shaping the factory of the future—insights from 500 manufacturers
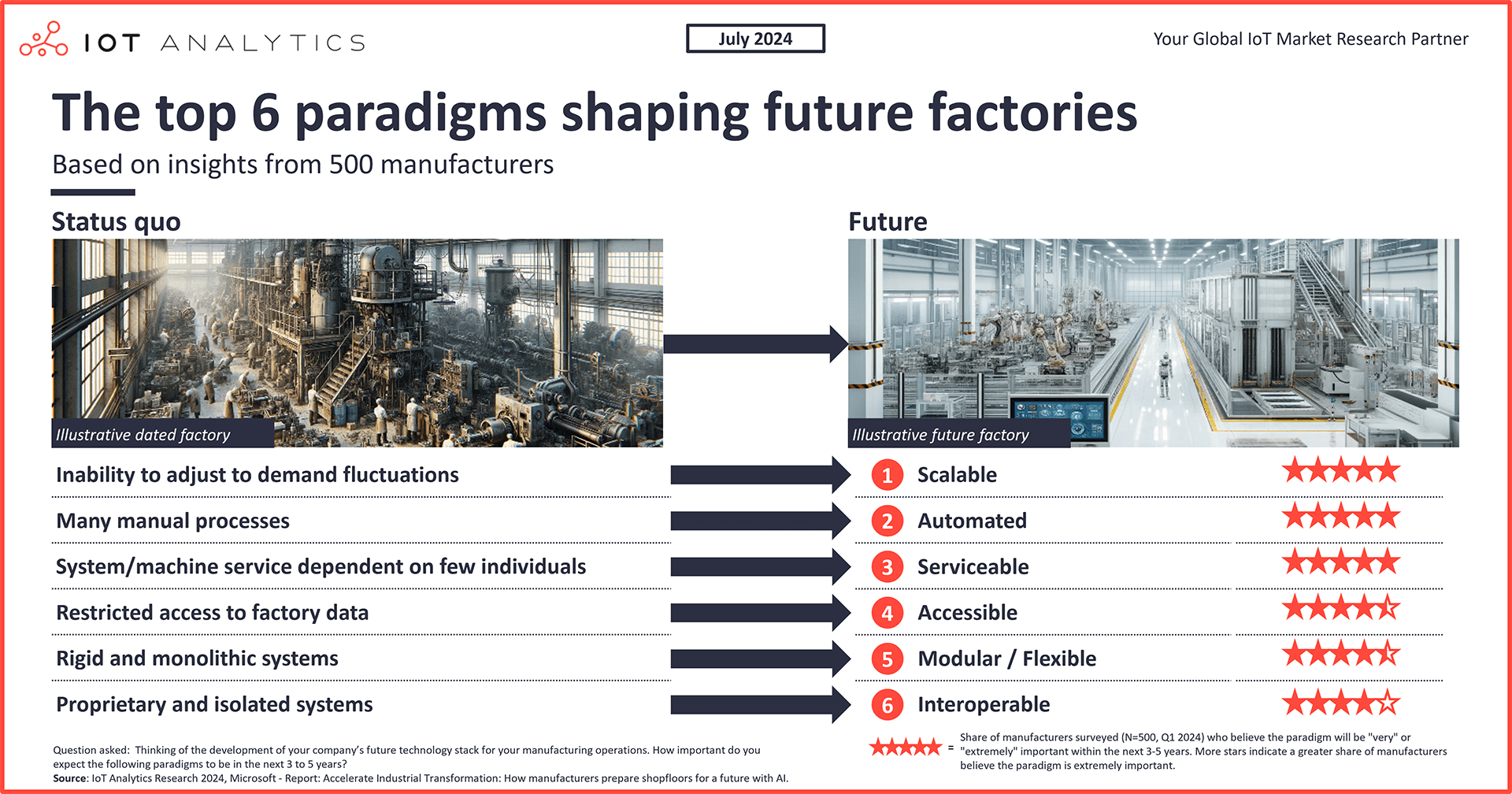
In short
- Amid record-high spending on factories, 6 paradigms currently define the factory of the future, according to the 52-page Accelerate Industrial Transformation: How Manufacturers Prepare Shop Floors for a Future with AI report, a Microsoft report with IoT Analytics the research partner.
- The automotive industry is setting the pace on industrial digital transformation, with BMW, Tesla, and Hyundai being prominent examples.
Why it matters
- For manufacturers: Understanding how peers see their future factory and operations can help manufacturers assess their own transformation strategies.
- For tech vendors: Staying apprised of how manufacturers see their future factories can help vendors align their offerings over the next few years and remain competitive.
Unprecedented investments in smart factories
Spending on new factories at record highs in the US. US manufacturers spent $193 billion on construction in 2023, according to the US Census Bureau. This spending represents a climb of 55% over 2022, when the US passed the Infrastructure Investment and Jobs, Inflation Reduction, and CHIPS and Science Acts, all of which intended to address inflation in the US and encourage the reshoring of key technologies, such as semiconductors, integrated circuits, solar panels, and batteries. As of May 2024, the seasonally adjusted annual rate for manufacturing construction spending climbed to $233 billion, reflecting a continued drive for manufacturing expansion through 2024.
Nearly three-quarters of manufacturers are transforming existing factories. Around the same time these acts were passed, Microsoft and Intel published IoT Signals – Manufacturing Spotlight, with the research conducted by IoT Analytics. According to the paper, 84% of manufacturers had developed smart factory strategies. These manufacturers developed their strategies in recognition that future operations and factories needed to be more flexible when faced with uncertainty and shifting market dynamics, as experienced during the COVID-19 pandemic.
The question becomes, how are manufacturers preparing for the factory of the future? What are they working to implement to handle turbulent market dynamics?
Recent market insights reveal how factories are transforming
Research into the factories of the future provides insights into how manufacturers are preparing for the future. In partnership with Microsoft, IoT Analytics conducted a global survey of 500 manufacturers in early 2024 to understand the latest trends, technologies, and priorities as they look ahead at the future of their operations, resulting in the 52-page Accelerate Industrial Transformation: How Manufacturers Prepare Shop Floors for a Future with AI report which is free to download on Microsoft’s website. The report provides insights from the manufacturers about how they envision their future operations, the challenges they face, and how they are preparing now to address these challenges by investing into technologies such as containerization, centralized device management, and industrial data ops solutions.
Note: Microsoft published a blog about the same report in June 2024, titled: 6 findings:manufacturers prepare their shop floors for AI.
Towards the factory of the future: The top 6 paradigms

6 key paradigms stand out for manufacturers. When asked to rank the importance of various paradigms within the next 3–5 years, the 500 survey respondents, on average, indicated 6 paradigms as either very or extremely important. In short, factories should be 1) scalable, 2) automated, 3) serviceable, 4) accessible, 5) modular/flexible, and 6) interoperable.
1. Scalability
Scalability matters most. 72% of respondents indicated that scalability—the seamless ability to expand and scale down in response to market demand—is crucial for their factories in the coming years. Scalable factories can replicate successful processes across multiple sites, improve efficiency, and reduce the need for significant reinvestment when expanding operations. This helps in maintaining a competitive edge in a dynamic market.
Voices from the industry
“The most challenging aspect for us, in regard to the adoption of technologies, is the standardization between multiple plants, countries, and regions.”
– Director of US-based automotive OEM overseeing optimization of manufacturing operations across sites
2. Automation
Automation augments and even replaces manual processes. 70% of respondents rated automation—using technology to perform tasks that were previously done manually—as either very or extremely important for their future factories. Automated factories can operate with minimal human interaction, leading to higher consistency and productivity. Automation also enables real-time data tracking and continuous improvement through advanced analytics.
Voices from the industry
“With automation on the shop floor, and especially our MES system to streamline workflows across the value stream, we can capture information about anomalies in machinery performance and aggregate this to generate analytics for continuous improvement.”
– Senior manufacturing IT manager at a UK-based food and beverage company
3. Serviceability
Serviceability helps companies overcome skilled labor gaps. 67% of respondents noted serviceability—the ease with which factory equipment and systems can be maintained and repaired—as very or extremely important over the next few years. When they say they prioritize the serviceability of their assets, they mean the assurance that their machines will keep running even during skill shortages.
As noted in the Accelerate Industrial Transformation paper, the Germany-based machinery manufacturer association VDMA found that 80% of manufacturing companies reported serious or noticeable bottlenecks due to skill shortages in 2022.
Voices from the industry
“Technology development nowadays is so fast that my team cannot always keep up.”
– Maintenance director of a South Korea-based engine manufacturer
4. Accessibility
Accessibility helps the workforce make the most of technological advances. 62% of respondents marked accessibility as very or extremely important for their future factories. Accessibility means providing easy access to factory data and controls, often through user-friendly interfaces and tools. Making technology accessible ensures that all employees, regardless of technical expertise, can effectively use and benefit from new systems. Accessible technology helps build a more skilled workforce, reduces training time, and enhances overall productivity, ensuring that important data and controls are readily available for decision-making.
Voices from the industry
“Making the technology accessible to people by developing skill sets is as important as the technology is for the OT environment.”
– Head of department at an India-based electric power generation, transmission, and distribution company
5. Modularity/Flexibility
Modular design and technology components ensure manufacturers remain flexible in the face of changing customer preferences. Approximately 58% of respondents see modular and flexible manufacturing—processes and systems designed to be easily reconfigured and adapted to new products or processes—as very or extremely important to their future operations. Flexibility allows manufacturers to quickly pivot to new opportunities or respond to changes in market demand without significant downtime or cost, and modular systems enable faster implementation of new technologies and processes, reducing time to market.
Voices from the industry
“Our highest priority is to integrate new software capabilities in a modular fashion. We want to be able to provide real-time updates on inventory and logistics to our customers now. So, we need to add a piece of software that is modular enough so it does not interfere too much with the rest of the system.”
-Vice president at a US-based food and beverages manufacturer
6. Interoperability
Interoperable systems reduce overall complexity. Finally, approximately 58% of respondents indicated that interoperability—the ability of different systems, devices, and applications to work together seamlessly within a factory—was crucial for their future factories. Interoperable systems enable more efficient data sharing and integration, leading to better coordination and optimized operations. With it, manufacturers can create a unified and coherent production environment, facilitating advanced analytics, improving decision-making, and supporting the implementation of new technologies like AI more effectively.
Voices from the industry
“When we adopt new technology, our main concern is about the integration and orchestration of different solutions. We need to face up different projects with different technologies in different regions, with different skills and resources.”
-Chief X officer at a Germany-based computer and electronic products manufacturing company
How companies are preparing for the factory of the future
Research for the Accelerate Industrial Transformation report found that companies leading the charge in realizing their factories of the future, among other priorities, do three things well:
- They manage devices efficiently with centralized device management. This involves managing industrial devices, including provisioning, certificate management, health and security monitoring, and updating from a single, central location.
- They use containerized OT software. Containerizing software workloads allows new or updated applications to contain all the necessary elements to run consistently at the edge or in the cloud, no matter where they are installed.
- They unify the data estate with industrial data operations. This involves standardized data integration in a place where everyone can access it. Industrial data ops are key technologies that manage and improve data flow, quality, and value within an industrial context
Leading adopters of future factory technologies
Automotive OEMs are among the most advanced. According to the report, the automotive industry sets the pace for industrial digital transformation. 100% of respondents from automotive manufacturers and suppliers reported that their organizations have containerized workloads, and 93% reported that their organizations are using at least one device management solution.
Respondents shared that three automotive companies in particular are prime examples of transforming their factories for the future: BWM, Tesla, and Hyundai.
1. BMW
“BMW is very much ahead in the adoption of containerization. They have reduced their operational expenses by approx. 50 %, I believe, which is very appreciable, and digitally, they have achieved a very big milestone.”
– Corporate IT director at a Singapore-based lifting and handling equipment manufacturer
2. Tesla
“Tesla has achieved large-scale battery production increases, leveraging AI to help detect issues and quality in manufacturing. They have achieved a very big milestone.”
– Manufacturing director at a US-based manufacturer of electronics and optical products
3. Hyundai
“With the help of centralized device management, [Hyundai was] able to remotely monitor equipment health, energy consumption, and performance of their manufacturing plant.”
– Senior production manager at a Japanese power company
More about how manufacturers are preparing for the factory of the future
Downloading the “Accelerate Industrial Transformation” report
These 6 paradigms are only a snapshot of the numerous insights in Accelerate Industrial Transformation: How Manufacturers Prepare Shop Floors for a Future with AI (free download via Microsoft). Along with reading the full report for more information about these paradigms, manufacturer challenges, and building blocks in realizing the factory of the future, IoT Analytics encourages readers to learn more about industrial digital transformation from recent research and reporting.
More IoT Analytics research on the topic
Related market reports
- Industrial Connectivity Market Report 2024–2028
- Industrial IoT & Industry 4.0 Case Study Report 2023
- IoT Enterprise Projects Adoption Report 2024
- Data Management and Analytics Market Report 2024–2030
- Equipment as a Service Market Report 2024–2028
- Generative AI Market Report 2023–2030
Upcoming market reports
IoT Analytics plans to publish several related reports in Q3 and Q4 2024:
- IoT Use Case Adoption Report 2024
- IT/OT Convergence Report 2024
- Industrial Software Landscape 2024
- Industrial AI Market Report 2024 – 2030
Related blogs
- The top 15 smart factory KPIs: Operational indicators most important for measuring performance
- Top 10 industrial technology trends—as showcased at Hannover Messe 2024
- Top 5 enterprise technology priorities
- Predictive maintenance market: 5 highlights for 2024 and beyond
- Industry 4.0 check-in: 5 learnings from ongoing digital transformation initiatives
Related market data
You may be interested in the following IoT market data products:
- Global IoT Enterprise Spending Dashboard
Are you interested in continued IoT coverage and updates?
Subscribe to our newsletter and follow us on LinkedIn and Twitter to stay up-to-date on the latest trends shaping the IoT markets. For complete enterprise IoT coverage with access to all of IoT Analytics’ paid content & reports including dedicated analyst time check out Enterprise subscription.
Leave a Comment